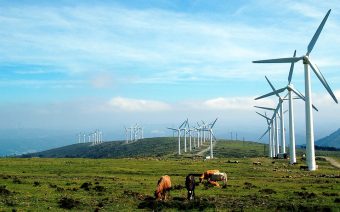
Wind turbines have increased in size and quantity to meet clean energy capacity demands
Modern wind power converts the kinetic (movement) energy from wind into mechanical energy. This happens through the turning of large fiberglass blades, which then spin a generator to produce electricity. Wind turbines, as they are known, can be located onshore or offshore.
Wind power is projected to continue growing across the U.S. by 2050. The latest Wind Technologies Market Report prepared by Lawrence Berkeley National Laboratory found that wind energy prices are at all-time lows, and for 2019, 7.3 percent of utility-scale electricity generation in the U.S. came from wind. In this blog post, we will examine land-based wind turbines and the recycling opportunities that exist but are not yet widely implemented for the turbine blades.
Wind turbine designs have evolved over time to increase in size and efficiency, ultimately leading to greater generating capacity. The principle design of commercial turbines today are horizontal axis wind turbines consisting of a rotor with three fiberglass blades attached to a hub, which is itself attached to a central piece (the nacelle) that is mounted on a steel tower. Various other machinery and concrete foundations are also included in modern wind turbine design, which include over 8,000 parts per turbine.
Wind turbine blades in the existing U.S. fleet average around 50 meters in length, or about 164 feet (approximately the width of a U.S. football field). And with recent trends to use longer blades on bigger turbines and taller towers to increase electricity production, a few of the largest blades produced today reach 60–80 meters in length.
In terms of durability, wind turbines last an average of about 25 years. About 85 percent of turbine component materials — such as steel, copper wire, electronics, and gearing — can be recycled or reused. But the blades are different as they are made up of fiberglass (a composite material) to be lightweight for efficiency yet still durable enough to withstand storms. The mixed nature of the blade material makes separating the plastics from the glass fibers to recycle into a workable fiberglass material difficult — and the strength needed for the blades means they are also physically challenging to break apart.
More:
Where do used wind turbine blades end up now?
Wind turbine blades require disposal or recycling when the turbines are decommissioned at the end-of-use stage, or when wind farms are being upgraded in a process known as repowering. Repowering involves keeping the same site and often maintaining or reusing the primary infrastructure for wind turbines but upgrading with larger capacity turbines. The blades might be replaced with more modern and typically larger blades. Either way, the fiberglass blades, once they’re no longer needed, pose the greatest challenge to end-of-use considerations for wind energy.
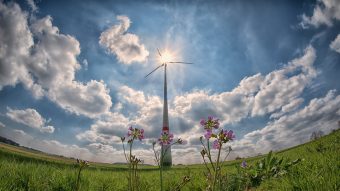
While it’s possible to cut the blades into a few pieces onsite during a decommissioning or repowering process, the pieces are still difficult and costly to transport for recycling or disposal. And the process of cutting the extremely strong blades requires enormous equipment such as vehicle mounted wire saws or diamond-wire saws similar to what is used in quarries. Because there are so few options for recycling the blades currently, the vast majority of those that reach end-of-use are either being stored in various places or taken to landfills.
Indeed, Bloomberg Green reported earlier this year on wind turbine blades being disposed of in landfills. Even though the waste stream represents only a tiny fraction of U.S. municipal solid waste, it’s clearly not an ideal situation. As wind turbines are being decommissioned or replaced, the necessity arises for more creative recycling solutions for used blades.
The good news is that some efforts at developing alternatives are underway. Two large utilities in the US, PacificCorp and MidAmerican Energy, for example, have recently announced plans to partner with the Tennessee company Carbon Rivers to recycle some of the utilities spent turbine blades instead of landfilling them. The technology used by Carbon Rivers is being supported through grant funding by the U.S. Department of Energy and will be used to break down and reuse fiberglass from used turbine blades.
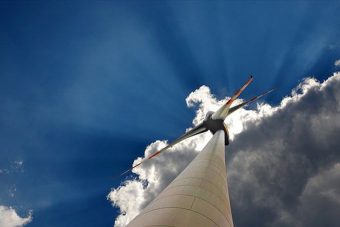
While the composite nature of fiberglass turbine blades makes them notoriously difficult to deal with at the end-of-use stage, interest in finding alternatives can also spark creativity and innovation. For example, a partnership involving US, Ireland, and Northern Ireland Universities called Re-wind developed some interesting civil engineering project ideas for reusing and repurposing fiberglass blades. These include using decommissioned blades in civil engineering projects as part of powerline structures or towers, or roofs for emergency or affordable housing. In Northern Ireland, Re-wind is also considering piloting them for use in pedestrian bridges along greenways.
Further down the waste hierarchy, additional recycling options are beginning to emerge. Wind Europe, representing the European Union’s wind industry, is partnering with the European Chemical Industry Council (Cefic) and the European Composites Industry Association (EuCIA) to develop new methods to reuse blade materials. The organizations estimate that 14,000 wind turbine blades will be decommissioned over the next few years in Europe alone. In May 2020, the consortium produced Accelerating Wind Turbine Blade Circularity, a comprehensive report which details design, research, and technical solutions focused on the wind turbine life cycle.
A key consideration for recycling of composite materials is to ensure that the recycling process has a net positive result compared to the alternative of disposing in landfills. One example comes from Germany, where the concept of recycling turbine blades into cement was first developed about a decade ago through a plant built under a partnership between Geocycle, a business unit of the building materials corporation HolcimAG, and the company Zajons.
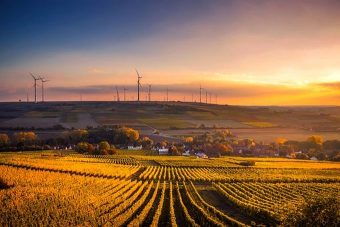
This form of recycling involves control of the disposal supply chain — including sawing the turbine blades into smaller pieces at the decommissioning site to decrease transportation logistics and costs. The process promises 100 percent recycling and reductions in carbon dioxide emissions from cement co-processing through replacing production of cement raw materials with the recycled blades, plus the use of biogas from organic remnants in place of coal as a fuel.
Other technologies such as mechanical recycling, solvolysis, and pyrolysis are also being developed, which will ideally provide the industry with additional options for handling fiberglass blades when they reach end-of-use.
Another creative recycling option produces pellets or boards that can be used in carpentry applications. In 2019, Global Fiberglass Solutions began producing a product called EcoPoly Pellets in the U.S. and will soon additionally produce a panel version. These products are certified as being recycled from decommissioned wind turbine blades through radio-frequency identification (RFID) tracking from the blade to the end-product. EcoPoly Pellets can be transformed into a variety of products such as warehouse pallets, flooring material, or parking bollards. Based on its demand forecasts, Global Fiberglass Solutions anticipates being able to process 6,000 to 7,000 blades per year at each of its two plants in Texas and Iowa.
An added approach to the blade recycling issue is to focus on the upfront piece — what the blades are made of. Additional research and development is looking into using thermoplastic resin instead of fiberglass or carbon fiber for wind turbine blades. The material may be easier and cheaper to recycle.
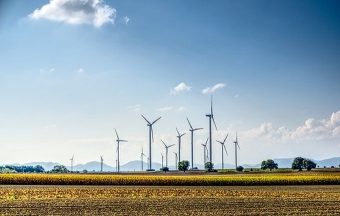
In the end, the goal of increasing innovation towards additional use applications for retired turbine blades requires having enough market demand to incentivize the creation of facilities that can recycle the blades. Alongside that challenge is a lack of policy in the U.S. regarding end-of-use considerations for turbine blades, further contributing to the status quo of storage or disposal as solid waste in landfills.
Achieving 100 percentage recyclability of wind turbine systems
As discussed above, it is currently less expensive to dispose of wind turbine blades in the closest landfill rather than the oftentimes long-distance transport required for recycling in the limited number of facilities that can process them efficiently. The industry, in addition, currently suffers from a lack of regulatory pressure or market incentives to fully develop other end-of-use options.
Two approaches to a more circular economy are greater communication along the wind turbine supply chain, and ambitious goals. For example, Vestas Wind Systems A/S, a wind turbine design, manufacturing, and global installation company, announced a bold commitment to produce zero waste wind turbines by 2040. The company plans to achieve this by increasing recyclability over the next 20 years through working closely with its partners along the supply chain to ultimately avoid any incineration or landfilling of its products. More partnerships like these between wind industry companies are needed to help fill the gap and make wind energy systems 100 percent recyclable.
Also, U.S. states should consider policy mechanisms to drive market development of alternative solutions, such as increased producer responsibilities, beyond the disposal of wind turbine blades in landfills. States could additionally contemplate ways to support construction of regional recycling infrastructure — particularly in states with larger portions of wind power such as Texas or Iowa — to address the end-of-use stage for wind turbine blades.
Source: CleanTechnica