Recycling raw materials mostly have limited use, especially when it comes to glass. Although it is generally thought that new glass products, which are of the same structure (such as jars, bottles, cups, etc.) are obtained from waste glass packaging, it is widely known in the scientific community that the range of application is much wider. At the Faculty of Technical Sciences in Novi Sad, within the framework of the doctorate with a very clear title “Model of the use of waste glass packaging as secondary raw material in the production of clay blocks” whose author is Zorica Mirosavljevic PhD, is precisely about the new application. Motivated by years of work on waste management, which goes back to the time when she was just a kid, Zorica decided to turn her enthusiasm into science.
EP: In Europe, whose trends we are striving to adopt, glass is treated as a recycling raw material in a closed cycle – we get glass packaging products from recycled glass. Various financial instruments stimulate recycling. What is the case with such practice in Serbia?
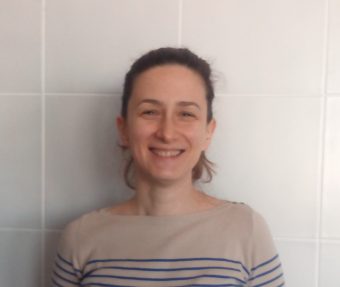
Zorica Mirosavljevic: The amount of glass has increased significantly over the last 20 years. Changing lifestyles and habits came with new age and integration into the consumer society. Few people think about reusing packaging, as our grandmothers and mothers used to do when preparing winter stores. We buy, consume and discard, and therefore the amount of waste increases. And that’s why we think about recycling intensely.
In particular, 85 per cent of glass in municipal waste is made up of glass packaging, and when it comes to recycling, that is the exact glass packaging that we have in mind. Of all types of glass, glass packaging is the most important during the management of municipal waste, and only glass packaging can be recycled by re-melting to obtain new glass packaging. This circular recycling process is fantastic because it saves on raw materials and energy by as much as 80 per cent than producing new glass packaging using only natural raw materials. In practice, unfortunately, due to the inadequate level of separation of glass packaging from municipal waste, it is difficult to come up with some more representative quantities that can be handled. Most glass packaging is intermixed when it comes to different colours of glass (white, brown, green), so it is difficult to recycle and reuse it for the production of glass packaging. The reason is that the melting temperature of the glass varies depending on the colour of the glass. Sorting the glass by colour further complicates the process, and it is necessary to have a developed system for collecting glass packaging, so in developing countries, therefore, most of the glass packaging most often end up in the landfill. That is why, according to European-level statistics, Serbia is in a very low place in terms of how much it recycles glass packaging and how it complies with European directives.
In Serbia, on the other hand, the low recycling rate for glass packing is primarily due to the low purchase price of glass, the high cost of collecting and transporting waste glass packaging and the very high cost of sorting glass by colour, which is necessary in order to use it as a secondary raw material in the production of new glass packaging. From an environmental point of view, this represents the best possible management option for glass packaging. As glass generally has high chemical and thermal stability, its degradation at landfills is negligible, which in turn creates a major problem at landfills. Technology that would provide a higher level of separation costs a lot, and there is no financial incentive in the form of subsidies or the form of waste disposal fees. The increasing amount of that glass in landfills is a consequence of this policy.
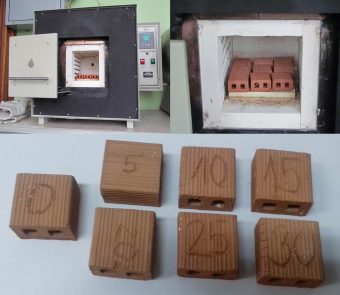
EP: What is the model of the use of waste glass that you worked on as a part of your scientific work?
Zorica Mirosavljevic: When Profesor Dragana Strbac PhD, my PhD mentor, and I decided to start finding alternative uses of waste glass, we first collected a certain amount of packaging and ground it to characterize the material. At the same time, we concluded that in brickworks across Serbia, there is a problem with the quality of clay used as a raw material for making construction products. If the amount of moisture in the raw material used in the production of ceramic products is increased, a large amount of energy is consumed to make a product that satisfies the market.
The experiment was set up to find a solution to these two problems, and we soon came to interesting conclusions. A detailed analysis of the current situation revealed that by adding glass and homogenizing a mixture of clay, we obtain a product that is better, more durable and with less moisture than the primary product. Both clay and glass contain a large amount of quartz which can be used. Increasing quality is just one of the positive factors in this process of obtaining a construction product. Of course, energy savings have been generated during this process. It is achieved by lowering the drying and baking temperature of the final product, which is made up of a mixture that is saturated with waste glass recyclate to some extent.
EP: The first analyses were carried out as part of the project “Using Waste Glass Packaging from the Landfill in Novi Sad as a Secondary Raw Material for Brick Production” which was approved at the provincial level, and later the continuation of the research is carried out as part of your doctoral dissertation. How far have you come now when everything has taken on a practical dimension?
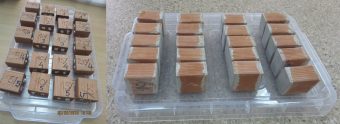
Zorica Mirosavljevic: For everything to make sense, it was necessary to present the project as technologically and industrially possible. Therefore, it was required to comply with some of the following conditions. When making clay blocks, we wanted to simulate the conditions that take place while obtaining construction products in brickworks. Firstly, the temperature range of the process was defined. The glass does not melt below 800 °C, and the baking of ceramic products usually takes place above 1000 °C, depending on the quality of the input raw material – clay. After that, we began to determine the size of the glass beads that are most suitable for mixing. The optimum size was below 0.71 microns. The next item was to determine the percentage of mass fraction of glass powder in the clay mixture. According to scientific papers published abroad, we reach a range of 0 to 20 per cent, while within our study, the range was expanded to 30 per cent by weight of glass powder, to see what is the most suitable composition of the mixture by checking the properties of the obtained experimental samples that would meet market standards. The first results are in favour of increasing the strength and reducing the moisture of the resulting product. According to the final estimates, the material has been obtained whose service life has been extended by more than 25 per cent. The part we should be practically working on, perhaps in the next project, is to reduce energy consumption. The brickworks in which we did the experiments reduced their temperature production process to 880 °C, due to the quality of the clay, so we could not overly influence the energy aspect here. According to scientific papers from the United Kingdom, it is estimated that up to 20 per cent of energy savings can be achieved, depending on the mass fraction of glass. It is up to us to check this in practice when the conditions allow us.
Interview by: Mladen Rajic
Read the whole article in the new issue of Energy portal Magazine GRINNOVATIONS, December 2019 – February 2020.